What shall I do to add cheerfulness and function to the ceiling of this residence Music Room?
The home owner has lost patience with a Good Earth Lighting, Model No. G4150_BN-I luminaire of superseded design needing impossible-to-find ballast and using two hard-to-find 26 watt CFL bulbs with plug-in base. Dim, not pretty, not bug-proof, more than $150 already invested.
I want to illuminate the entire room uniformly. with LED lights distributed upon the nine-foot ceiling. In Winter 2016, choose Nicor DLS4 , 671 lumens.
Pegasus Lighting offered this free advice, prominent in Google search:
Helpful rules for lighting placement:
How To Layout Recessed Lighting In 4 Easy Steps
Lesson 3:
To determine how far apart to space your recessed lights, divide the height of the ceiling by two.
Lesson 4:
Make sure to place recessed lights approximately three feet away from the wall.
Here is another set of rules, inviting in its avoidance of word "recessed:"
Downlighter Spacings
The Chartered Institute of Building Services Engineers, CIBSE, is cited, from London:
CIBSE code for interior lighting .
For this 10' by 15' residence Music Room, choose: Illuminance = up to 300 lux. Five 671 lumens Nicor DLS4 well-placed is suited to CIBSE advice.The Music Room area is 14.5 sq meters. Average illuminance is 5*671/14.5 = 231 lux.
(I overlay plans on a satellite photo of the home.)
As noted, lighting that began with Nicor DLS4, 671 lumens each, 3000°K in a Music Room, became all Utilitech 0752125, 700 lumens each, 3000°K. The 4" DLS4 lights were uncomfortable to gaze upon.
Discuss the initial installation of Nicor DLS4:
Despite attention to advice, proceed with caution. Mount lights temporarily. Flatten the ground tab of each box-mounting bracket and attach to the ceiling by a single drywall screw, loosely set.
One bracket center is of the found light. Four more were mapped by the rules.
The pigtail of each light is accessible to bell wire attachment.
Let there be temporary light, on-approval overnight.
At positions now-committed, trace and cut in RACO 175 junction boxes.
I have generously used pencil markings. All excess markings are gently erased in scrubbing with wet flexible grout.
Use a jab saw for junction box cuts.
Use a handsaw for access cuts.
Take care to not drop the access drywall, that must be reset.
After much mapping of nails with a strong magnet there are no surprises. The single romex wire of the found light has troublesome staples that must be pulled. The wire end will be pulled back, to first serve the box beyond the access cut seen in this photo.
Mass-produce box supports.
Some care is needed to affix a Nicor DLS4 to its bracket. Clips deform often with the difficult blind push, coping with lead wires.
The access patch is time-critical, with setup time needed in repeated application of flexible grout. Taping is never needed with well-supported edges and flexible grout. The entire ceiling would need leveling and new texture, if dryall tape were employed.
Just vee all patch edges to a 3/32" gap.
The still-wet access patch shows in this photo, but will be invisible after the ceiling is next painted. This is good progress toward a better future of starry skies lighting. Lights will be beautiful crystals, not recessed, less bright than this. I wish for a 450 lumens unit of light, a pattern of about eight lights in this room. No 450 lumens luminaires are on-offer. When they are, let there be a sprinkling too of 300 lumens lights to randomize patterns. Maybe a brighter light now and then, to further randomize. I wonder if we will find alternatives to fairly aggressive cuts, and patches, for access. This access cut is in fact quite small, where I could count on directing wires via 3 1/2" cuts for junction boxes. I wish for low voltage wiring of lights without junction boxes even; but have things to learn about fishing such wires blindly.
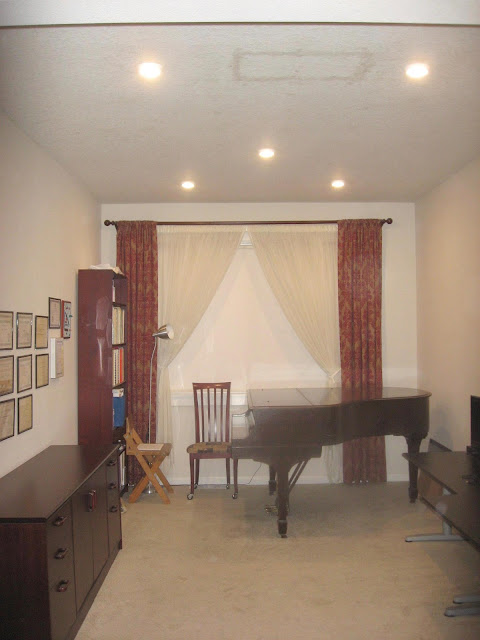
At 3/20/2016, report disappointment with the tried Nicor DLS4 lights. I find that they are too bright to look at, even on a nine-foot ceiling. The DLS4 lighting density, lumens divided by circle of intense light, is higher by about half, vs. Nicor DLS56 or Utilitech 0752125, amounting to design error in Nicor DLS4.
Utilitech 0752125 have replaced the Nicor DLS4, brightening the room by 4%, while being much easier to look at. The lights with less glare are less confusing to a camera too, evident in better focus.
Utilitech 0752125
Nicor DLS4
This is what happens when R19 kraft-faced batts are stapled to floor sheathing, in a crawl space with framing 4x8@48, so hard to insulate. Twine everywhere just densified the jungle. It was much worse before a couple of rounds, carting away fallen-down batts; really ugly.
Many generations of mice thrived atop the kraft facing and in falling-down caverns.
Half of the batts did not share this decrepitude, sadder then to pull them down for disposal.
About 1200 gallons of compacted batts were sent off to an Eastern Oregon landfill, via this transfer station and rail cars. This is one carload of 250 gallons, a crime, but nothing compared to a mountain of plastic foam that should have had an alternative use.
HVAC ducting came into view, this an awfully-leaky 14" return line. All other ducts were Thermaflex flex, far more to be hated, as probably the major cause of the vermin infestation, the magnets of the post title.
The flex ducts were to be hated for their thoughtless construction. Here a duct is partially detached where it stressfully ducked under a water pipe.
In imagining how to craft vermin-proof new crawl space insulation, consider a romex lead to a living room floor outlet. A competitor suggested spray foam, nicely ruled out by the wiring obstruction. At about this time I would confront a ruined very-expensive home in a sad bid visit, uninhabitable due to stink of foam, white hardness coating even the ground.
Horrible decrepitude of the flex ducts was not easily seen. A Northwest corner of the crawl space, least accessible, was littered with rat traps. Why?
Where my discoveries began in Mid-July, 2015, my mandate was just to fix the ruined insulation. I spent part of a day pulling down batts. Then I brought lumber and insulation, to try out a method that had been on-my-mind for years. Here it is:
And with adjusted attitude and method, it works. But, what of interfering ducts? I'm told I must cope with them. I have impending family travel, and a Summer of air conditioning is wanted. I will return, and will find workable paths, in Early-October.
It is late-September, and I will attack the ducts, not really authorized. This is the near duct I had crushed, thought to be attached OK. The liner has a leak, but there is much worse. See the detached spring coils? All Thermaflex ducts in this home are of an early, brittle polyethylene formula. Wires are detached. There are associated liner rips, everywhere.
I expected decrepitude at the thoughtless runaround of laundry water pipes. Curse that damned "duct tape!"
See lots of leakage in the steel piping. See a large separation in the plastic liner, that had been hidden but not blocked, by insulation lining.
See more detached wire, and holes everywhere, inside the flex duct.
Everywhere, is not much exaggeration.
A D-box is a hydraulic monster, itself with usually-leaky attachments.
Incredible.
And, Thermaflex will poo poo, chemistry from mice somehow caused this.
This was the main entry to ducting by rats and mice, then having access to the house interior. The foulness of the liner is evident. Yet a pest abatement contractor spliced in an oversize aluminum flexible duct as the sufficient cure years ago.
Within the insulation lining, not before explored, I found this. The stick was within the air path. With the report I found immense home owner gratitude that I had insisted on demolition and re-imagined ducts.
Crude D-Box tab-in collars can not be sealed.
An insulation-lined turning box replaces the D-box. Use springy lumber to gently find alignment.
A found strap is useful, the rest of the demolished D-box is recycling.
A 16-12-12 wye was an obvious need in this alternative to ridiculous job-hacked D-boxes. Aligning it for clearance of a nearby post is challenging. Begin to see thick flexible grout coating inside all unlined steel fittings, to isolate them somewhat from temperature cycles of carried air. If the steel does not fully swing with air temperature, it has important reduction of thermal mass. Most of the volume in flexible grout is insulative ceramic microballoons.
In a chosen wye orientation, bring on insulating wrap, and secure fittings with screws and UL181 Foilmastic tape.
Some of the weight of steel components is borne by cantilever from the turning box and furnace. Most weight is carried by taut wires at joining pieces.
In advance of each joining, pull on ample lengths of insulation jacket. Jacket should fully cover all steel and insulation.
Work now with the left-side 12" branch of the 16-12-12 wye. There is a quick 6" wye take-off to a register.
Note the excess liner lengths needed to contain all steel, insulated, out of sight.
Please rely on this diagram of the as-built ducts, to locate the work in following photos.
This attachment to a 12-12-6 wye is with necessary change of direction. Pull quite a bit of tension to limit flow resistance. Call the axial taping strain relief.
Here is finished appearance at the 12-12-6 wye, in a high-traffic area. Interleaving insulation and wrap from two directions can be bumpy.
This is the previously-hated low Northwest corner of the crawl space, close up. Leaving at end of an October day, the furnace is back on and all but two registers are served.
Back in the Northwest corner, for some clear-headed, intense duct construction.
Ducts all done, but to rework a branch warming the kitchen. I will leave some of this now-dirty OSB, though I don't expect ever to return.
Here is the Northwest corner at a distance, now not foreign or hated. I see the rocky dirt as dry. I will not bother to pull up ill-fitting black visqueen, over the rocks and concrete piers.
Survey the completed ducting, starting at the furnace. Yes, there is a rat trap down there, never to be needed again, soon to be gone and forgotten. Everywhere there is smoothness overhead, and I have been under there in the duct-running.
North wall alley. Just duck under, to get past the furnace.
The 16-12-12 wye at the furnace nicely split about a post. All weight is tied by wires to the beams above.
The 12" branch toward the kitchen is pulled over vent piping, off the ground, without much flow resistance at a formation to oval.
The house had a single 7" register for the kitchen, laundry and a little bathroom. Sadly resigned that can't be improved, minimize resistance to the 7" register, new, firmed-up. 8" flex duct transitions through a 7" reducer.
Kitchen HVAC duct finally done. In the distance, I will now finish an obstructing 6" duct from the kitchen grill and fan. Overhead see another approach to hard-covered vermin-proof crawl space insulation using rips of OSB.
A determined recycler, I took apart ducts belatedly hauled from the job, too dirty and bulky for hauling with bagged insulation trash. Recycle all metal, including spring coils chopped to about 12" lengths. Take a pause. Send that rat ridden end above for examination by Thermaflex in South Carolina.
Thermaflex was nice, accepting a length of the brittle liner for examination at my cost, against accusation failure is general; a cause of mouse and rat access, not a symptom, surely this not the only instance. To my shock and dismay, they would disagree with me, blaming mice as cause of embrittlement. And, they offered no comment whether current production is with better material.
Sharing this blog post then with Thermaflex, I studied their product claims. Theirs are guaranteed for ten years, said to be better than with competitors .These had "served" perhaps 25 years. What are we to expect past-warranty? Have materials improved in current production? We need to know these things.
Let's have some discussion here. What have others found? Will a manufacturer speak up about materials evolution?
I suggest to Thermaflex that I am worthy as a commenter, for teaching good flex duct installation practices. May we talk about this, too?